Optimization solution
for utilization frequency
Optimization solution for utilization frequency
The status of utilization of the transportation equipment is clarified and the maximum utilization of the equipment is supported by allocating it according to the actual usage conditions.
Understanding usage trends
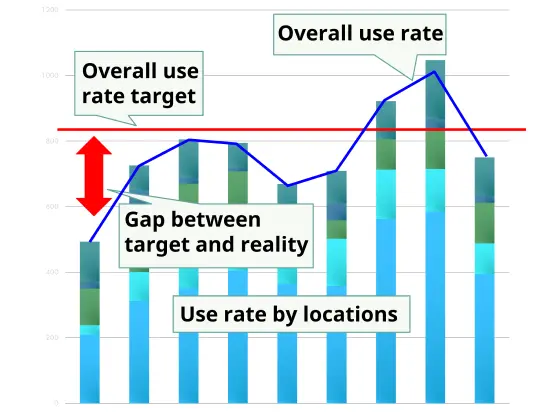
The usage status across all locations and at each location can be used to determine trends in the use of transportation equipment.
Analysis of status of utilization
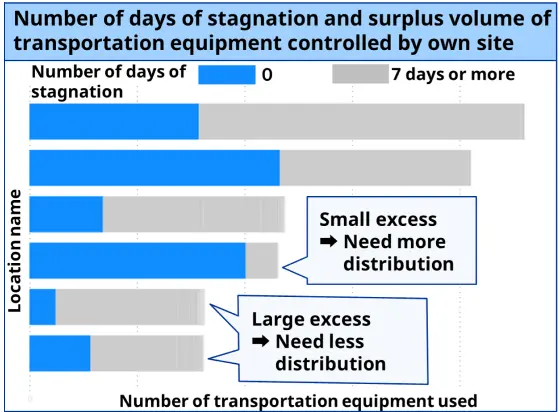
The count of equipment that remains for 7 days or more (indicating that there is sufficient transportation equipment at the location) can be used as a guide for the amount to be allocated to each location.
Clarification of off-purpose use
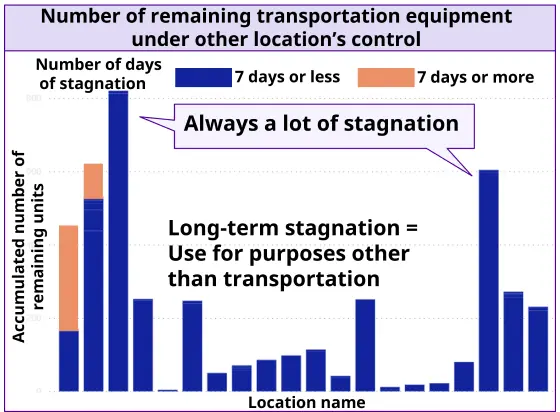
This information can be used to adjust for stagnation and uneven distribution to the location where the transportation equipment of other locations stays and is used for purposes other than its intended purpose.
Implemented examples
Alps Logistics Co., Ltd.
Alps Logistics, which provides various logistics services ranging from storage to transportation, import/export, etc., allocates and utilizes stacked racks at each location to increase the loading rate of trucks, but the frequency of use varies and the overall loading rate cannot be fully improved. Therefore, there has been a need to "check the number of times each location uses the racks" and "understand the number of racks that are left unused."
By introducing Alps Alpine's MonoTra™ solution, the number of times stacked racks are used at each location and the overall usage rate can be monitored, and by analyzing how long and how many racks remain at each location, uneven distribution can be eliminated, leading to improved usage rates and reduced stagnation rates. In addition, the increased use of stacked racks has led to an improvement in the overall loading rate, which has improved delivery efficiency and led to a reduction in CO2 emissions from transportation vehicles.